our Capabilites
Achieve your target products through our robust sheet metal processing equipment, technical expertise, and product experience. Over the past 20 years, we have assisted over 2500 clients in manufacturing various components, thereby reducing their budgetary costs.
Sheet Metal Cutting
Sheet metal cutting is a subtractive manufacturing process, as it enables the production of usable parts by simply removing material. Manufacturers can employ various methods to cut sheet metal, including laser cutting, waterjet cutting, and plasma cutting.
- High precision control
- Cutting up to 12 meters length
- Tolerance ±0.05 mm
- No abrasion or deformation
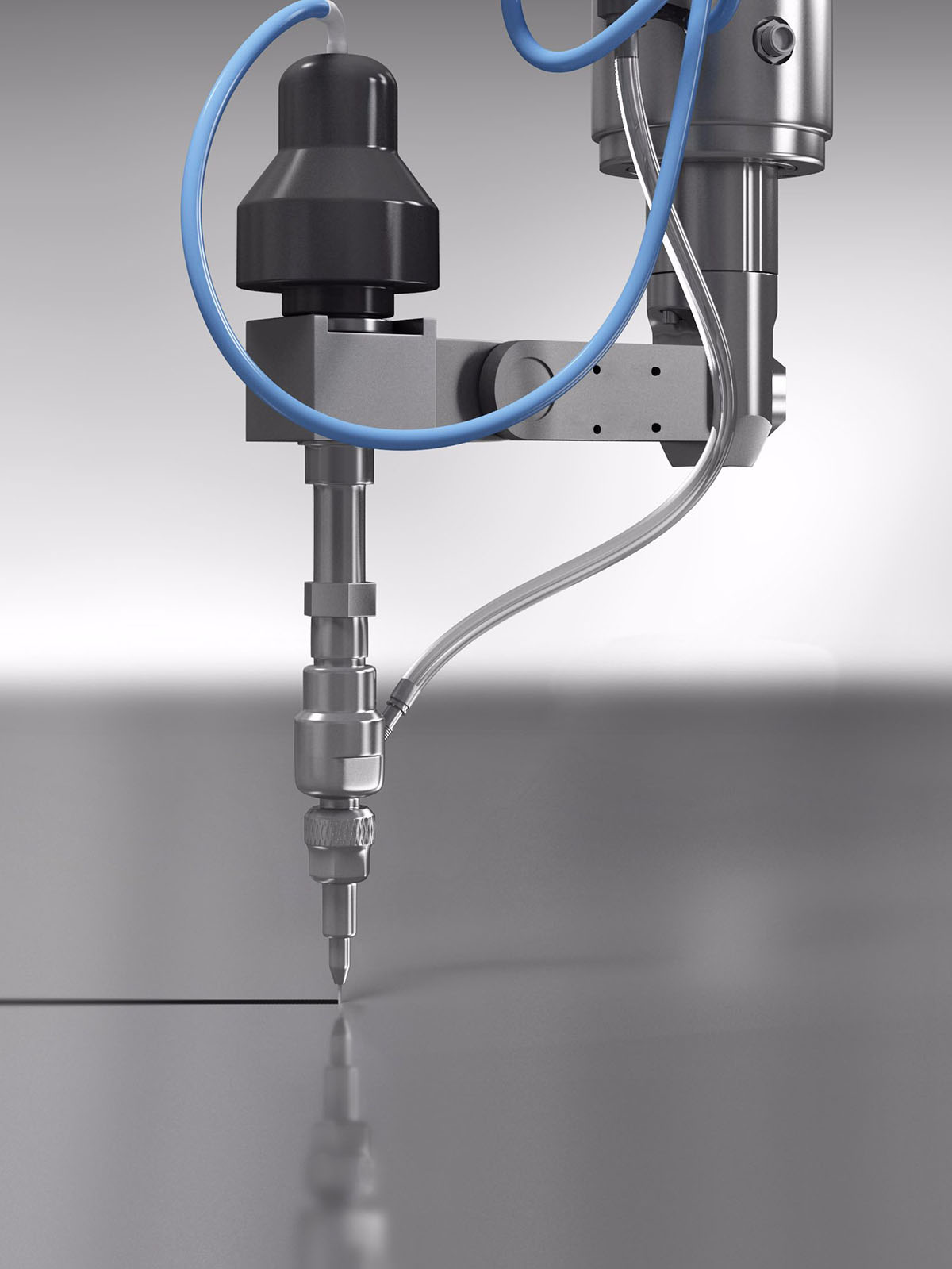
CNC Laser Cutting
Laser cutting uses powerful lasers enhanced by lenses or mirrors. It’s a precise and energy-efficient machine suitable for thin or medium-sized metal sheets, though it may struggle to penetrate the hardest materials.
Waterjet Cutting
Waterjet cutting uses high-pressure water jets to cut metal. It’s particularly effective for cutting low-melting-point metal sheets, as they don’t generate heat that could potentially cause metal to deform excessively.
CNC Plasma Cutting
Plasma cutting creates an ionized gas electrical channel, forming a thermal plasma jet that can easily penetrate thick metal sheets. While not as precise as laser or waterjet cutting, it’s fast, powerful, and costs less.
Sheet Metal Welding
Common welding methods for sheet metal parts include argon arc welding, resistance spot welding, CO2 gas shielded welding, and manual arc welding. They each have different applications and limitations.
Gas Welding
Gas welding melts metal parts using a flame from burning gas. It’s commonly used for joining thin sheets of steel, cast iron repairs, and non-ferrous metals like copper and aluminum.
Laser Beam Welding
Laser beam welding melts metal parts using a focused laser beam. It’s great for small or hard-to-reach areas, but it’s not widely used because lasers are expensive and not very efficient.
MIG Welding
MIG welding uses gas to shield the welding area, ensuring a stable arc and consistent quality. It melts metal parts with arc heat and feeds in a welding wire to join them.
Plasma Arc Welding
Plasma arc welding uses a high-energy beam to weld metals like tungsten, molybdenum, copper, nickel, and titanium, which are difficult to melt or sensitive to heat.
Spot Welding
Spot welding uses electrodes to create weld spots between overlapping metal pieces. Pressure and electric current are applied to melt the metal, forming welds.
TIG Welding
Tungsten Inert Gas (TIG) welding, is the most commonly used method for welding stainless steel sheets ranging from 0.5mm to 4.0mm in thickness, whether manually or automatically.
Sheet Metal Forming
Sheet metal forming is the process of shaping metal sheets into the desired shapes using molds. This includes two methods: cold forming and hot forming. Cold forming is suitable for thinner sheets, while hot forming is typically used for thicker or more complex parts. Forming can be used to create curves, bent edges, and various convex and concave shapes.
Sheet Metal Bending
Sheet metal bending is the process of bending metal sheets to the desired angle or shape. This step typically requires specialized equipment known as a press brake.
Sheet Metal Rolling
Sheet metal rolling is a metalworking process that involves passing a sheet of metal through a series of rollers to reduce its thickness or change its shape.
Sheet Metal Stamping
Sheet metal stamping is a cold forming process widely used in the production of automotive components. However, for small-scale production, the cost of tooling is proportionally high.
Machining Standards
The mature standards of sheet metal processing serve as the constraints for the forming of sheet metal products. This design specification specifies the processing requirements for bending and welding, applicable to all sheet metal products designed and manufactured by our company.
Limit Deviation Values for Linear Dimensions
Processing Type | Basic Dimension Range (mm) | |||||
---|---|---|---|---|---|---|
0-30 | >30-120 | >120-400 | >400-1000 | >1000-2000 | >2000-4000 | |
Sheet Metal Bending | ±0.2 | ±0.3 | ±0.5 | ±1.5 | ±3 | ±4 |
Welded Parts | ±0.5 | ±0.8 | ±1.2 | ±3 | ±5 | ±6 |
Limit Deviation Values for Fillet Radius and Chamfer Height Dimensions
Processing Type | Basic Dimension Range (mm) | |||
---|---|---|---|---|
0-3 | >3-6 | >6-30 | >30 | |
Sheet Metal Bending | ±0.4 | ±0.3 | ±0.5 | ±1.5 |
Welded Parts | ±0.5 | ±0.8 | ±1.2 | ±3 |
Limit Deviation Values for Angle Dimensions
Processing Type | Basic Dimension Range (mm) | ||||
---|---|---|---|---|---|
0-10 | >10-50 | >50-120 | >120-400 | >400 | |
Sheet Metal Bending | ±1°30′ | ±1° | ±1° | ±30′ | ±20′ |
Welded Parts | ±3° | ±2° | ±1° | ±30′ | ±20′ |
Limit Deviation Values for Hole Spacing
Processing Type | Basic Dimension Range (mm) | |||||
---|---|---|---|---|---|---|
0-50 | >50-100 | >100-200 | >200-400 | >400-1000 | >1000 | |
Sheet Metal Bending | ±0.3 | ±0.3 | ±0.4 | ±0.4 | ±0.5 | ±1 |
Welded Parts | ±0.5 | ±0.6 | ±0.7 | ±0.8 | ±0.9 | ±1.2 |
Sheet Metal materials
The materials commonly used in sheet metal processing are as follows. The choice of material varies according to the product’s function and cost considerations.
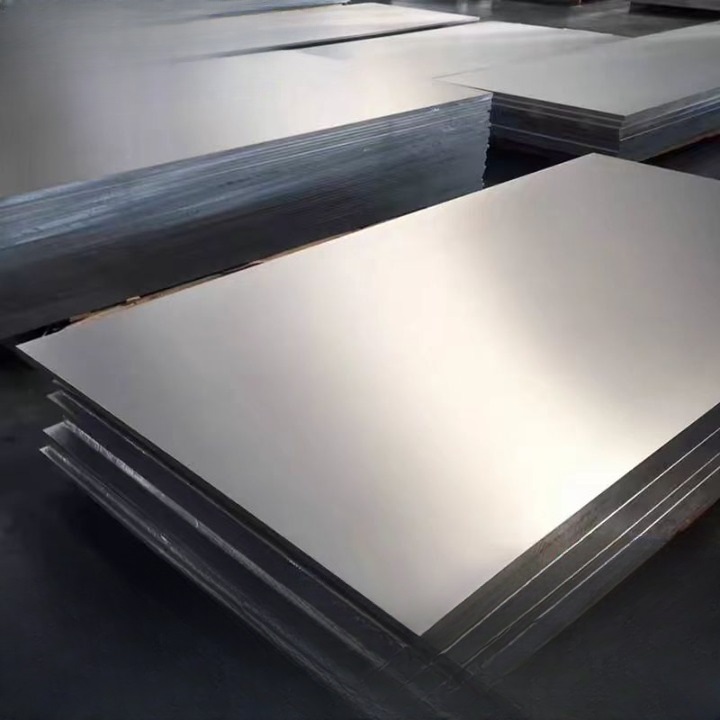
- Aluminum Plate
- Types: 6061、5052、1010、1060、6063
- Surface Treatments: Chromate (J11-A), oxidation (conductive or chemical), silver-plated, nickel-plated
- Advantages: High versatility, various surface treatment options
- Coated Aluminum-Zinc Sheet
- Coating Materials: Typically polyester, silicone-modified polyester, polyvinyl fluoride, etc.
- Advantages of Coating: Excellent weather resistance, heat resistance, corrosion resistance, and decorative properties.
- Cold-Rolled Plate (SPCC)
- Main Usage: Electroplating and baking paint parts
- Advantages: Low cost, easy formability
- Material Thickness: ≤3.2mm
- Copper (CU)
- Types: brass, bronze, beryllium copper
- Main Usage: Conductive parts
- Surface Treatments: Nickel plating, chrome plating, or untreated
- Advantages: High conductivity
- Galvanized Plate (SECC, SGCC)
- Types: SECC (N material, P material), SGCC
- Usage: SECC N material for untreated surfaces, SECC P material for spray-painted parts
- Advantages: Various surface treatment options
- Hot-Rolled Plate (SHCC)
- Main Usage: Electroplating and baking paint parts (primarily for flat parts)
- Advantages: Low cost, difficult to form
- Material Thickness: T ≥ 3.0mm
- Stainless Steel
- Types: SUS301, SUS304
- Surface Treatments: mirror finish, brushed finish, matte finish
- Main Usage: Untreated surfaces
- Advantages: Corrosion resistance, high durability
Why Choose us?
Our Advantages
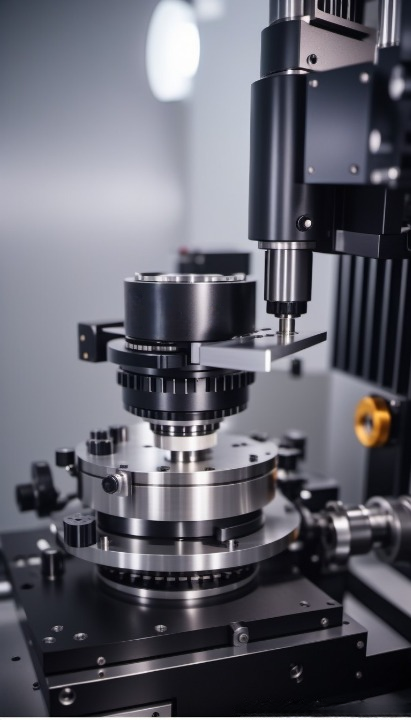
Rapid Prototyping
3-Days quick turnaround time to deliver prototypes.
Rich Production Experience
Over 500 experiences in developing molds for various applications.
Professional Team
A professional team of over 10 technical engineers ensuring high-quality output.
Comprehensive Solutions
One-stop solution provider catering to all customer requirements.
Cost-Effective Services
Offering competitive prices, reducing production costs by up to 50%.
High-End Equipments
Equipped with 18 machines for lathes, milling, laser cutting, and laser welding.
Ready to Access to Your Project?
Please tell us your project details, you can upload design drawings or other attachments. We usually respond to your quote request via email within 1 hour.
Related Terms About Sheet Metal Fabrication
Here are the terms sorted alphabetically from A to Z:
- Bending
- Blanking
- Chamfering
- Countersinking
- Drawing
- Drilling
- Embossing
- Expansion Riveting
- Flattening
- Forming
- Hole Enlargement
- Nutsert Installation
- Perforating
- Piercing and Tearing
- Punching
- Retapping
- Rivet Joining
- Rivet Pressing
- Riveting
- Shearing
- Stamping
- Straightening
- Tapping
- Undercutting
- Web Hole Punching
- CNC Router
Sheet Metal Applications
With sheet metal processing techniques, we can manufacture a diverse range of products such as chassis enclosures, machine tool housings, distribution boxes, control cabinets, network server cabinets, and precision automotive components.
Sheet metal fabrication is essential in architecture, offering versatile, durable, and aesthetically appealing solutions for facades and interior elements. With advanced technology and skilled craftsmanship, it delivers precise designs to meet architectural project needs.
Architectural Industry
Many electronic and household appliances use sheet metal processing for their enclosures and casings. Sheet metal enclosure and cabinet processing are two major aspects of this industry.
Electronic Products
Most car bodies are made with sheet metal processing due to its lower cost and ease of shaping and welding, ensuring vehicle strength. Charging stations for electric vehicles in the transportation sector are also made through sheet metal processing.
Automotive Parts
Medical equipment that requires sheet metal processing includes hydrotherapy equipment, medical testing devices, and beauty instruments.
Medical Devices
The shells of devices such as self-service ticket machines, vending machines, and self-service coffee machines are commonly made using sheet metal processing.