Introduction
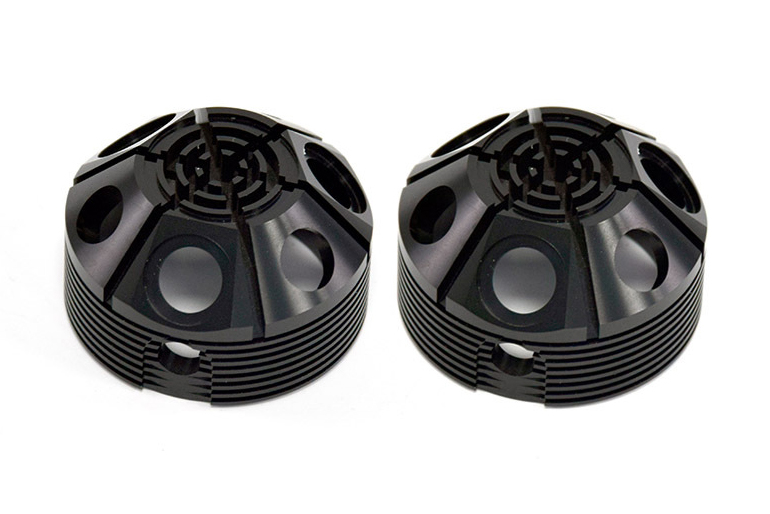
The FPV electronic equipment connector component is a well-designed circular object used in FPV (First Person View) electronic devices as a critical part for connection, support, or signal transmission. It features multiple concentric grooves and holes on its surface, ensuring unobstructed transmission of electrical signals, data lines, or other fluids, guaranteeing stable and reliable device performance. Additionally, its orderly and precise design ensures excellent performance during high-speed operation or in complex environments.
Manufacturing Specifications:
Objects | Value |
---|---|
Material | High-quality aluminum alloy |
Machining Dimensions |
Overall Diameter: φ50mm Overall Thickness: 15mm Large Circular Hole Diameter: φ20mm Small Circular Hole Diameter: φ5mm Groove Depth: 3mm Groove Spacing: 5mm |
Machining Tolerances |
Diameter Tolerance: ±0.02mm Thickness Tolerance: ±0.01mm Hole Diameter Tolerance: ±0.01mm Groove Depth Tolerance: ±0.01mm |
Machining Accuracy |
Surface Roughness (Ra): Less than 0.8 micrometers Hole Positioning Accuracy: ±0.01mm Smooth edges with no burrs |
Machining Equipment |
High-speed precision CNC milling machine CNC drilling machine Precision measuring instruments |
Surface Treatment | Anodizing, deburring |
Application Area | FPV devices such as drones, remote-controlled cars, etc. |
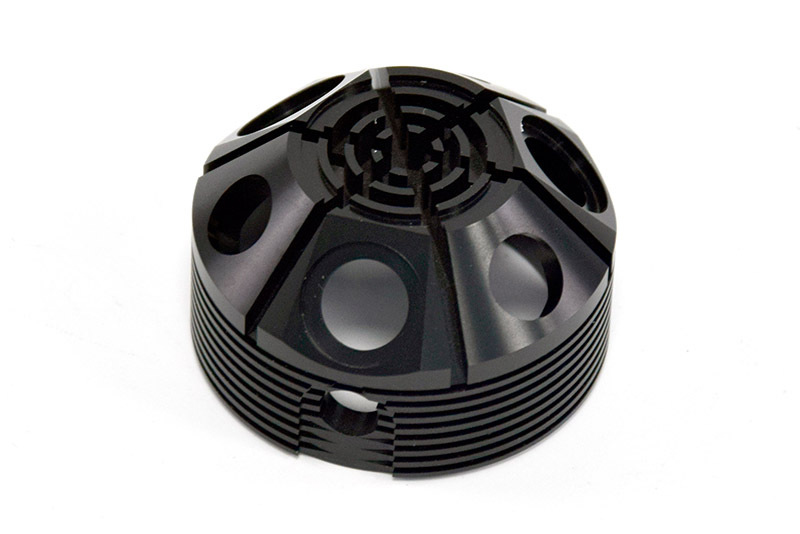

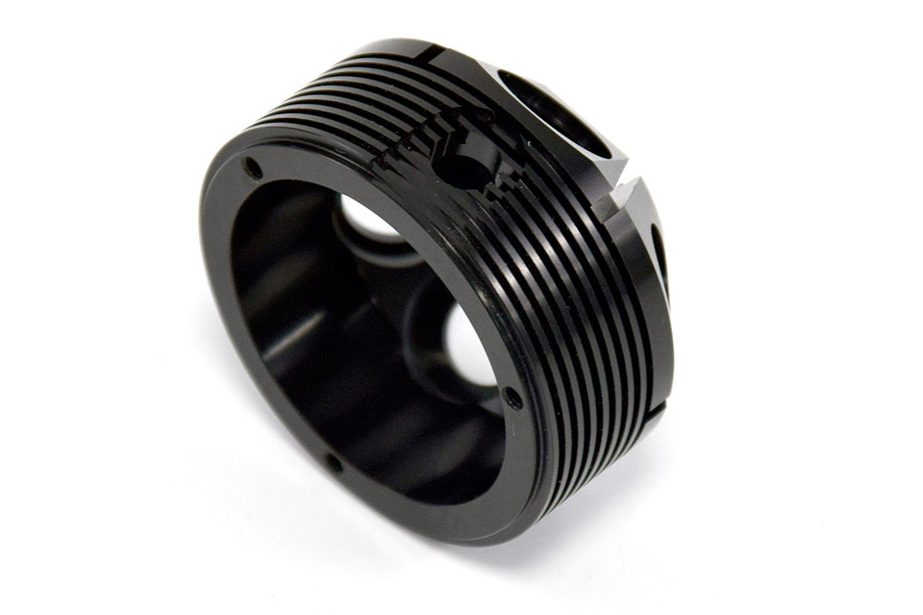
CNC Machining Process
a. Design Phase: The part’s three-dimensional model is first designed using professional CAD software, considering the performance and working environment of FPV devices, and detailed planning of the part’s structure, dimensions, and materials.
b. Programming Phase: Based on CAD design, machining programs are generated using CNC programming software to ensure accuracy and efficiency during the machining process.
c. Material Preparation: High-strength, wear-resistant metal materials are selected as processing raw materials to ensure the durability and stability of the part.
d. Fixture Design: Specialized fixtures are designed to ensure stability and accuracy during the machining process.
e. Machining Phase: The material is placed into CNC machine tools, and machining is performed according to the programmed process, including milling, drilling, tapping, etc., accurately machining each part of the component.
f. Quality Inspection: After machining, strict quality inspections are conducted on the part, including dimensional measurements, surface finish checks, etc., to ensure that the part’s quality meets design requirements.